Lattice structures have been extensively studied and experimented with, particularly in the last few decades with the advancements in additive manufacturing (AM). While various research focuses on investigating the tensile, bending, and fatigue properties of these structures, standardized tests for mechanical characterization are limited to compression testing. The only standardized tests so far are the compression tests listed in ISO 3386 (polymers) and ISO 13314 (metals). Compression tests primarily provide compression stress-strain curves to understand the load-bearing properties and design characteristics of lattice structures. Key metrics derived from these tests include stiffness, yield strength, plateau stresses, compression at specific strains (e.g., 30% or 40%), maximum absorbed energy and densification strain as illustrated in Figure 1.
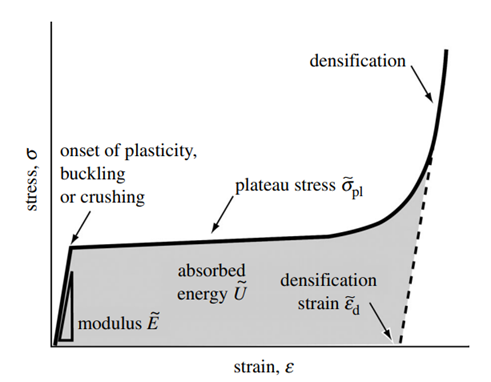
Numerical Simulation:
Numerical simulation is a valuable tool that helps reduce reliance on experimental methods for mechanical characterization. However, it requires a validated material model that accurately represents the properties of the lattice structure. Although some variation between numerical and experimental results is expected due to inherent defects in most AM processes, numerical simulations remain an effective way to understand the mechanical behavior of lattice structures and significantly reduce trial and error attempts to achieve desired mechanical properties.
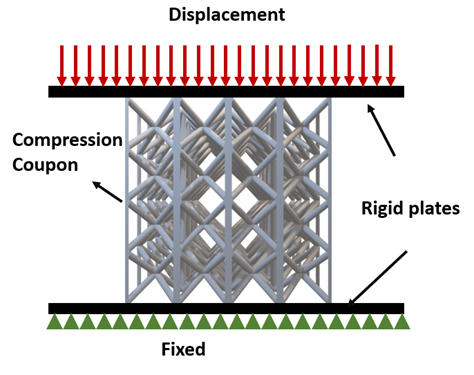
The most typical boundary conditions are shown in Figure 2. For quasi-static compression simulations, explicit solvers are more efficient, particularly for 3D problems with self-contact and large deformations. Strategies such as artificially increasing the speed of the process by reducing the time scale or increasing loading rate, as well as mass scaling the material, can be considered to obtain an economical solution. However, it is crucial to ensure that the kinetic energy remains negligible compared to strain energy.
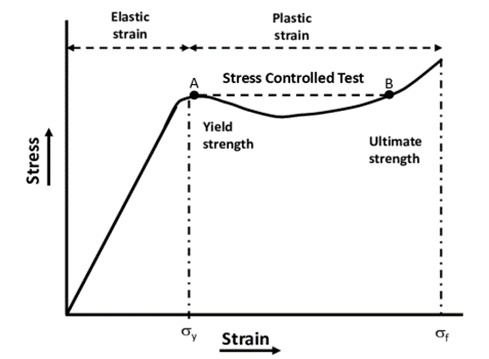
When obtaining stress-strain curves, displacement-controlled tests are more common. These tests allow for obtaining typical stress-strain diagrams where stress decreases after reaching the yield point. Stress-controlled tests are not suitable for this type of analysis, as stress would continue to increase with time as shown in Figure 3.
Metafold's Approach to Lattice Structure Simulation:
Metafold empowers engineers and researchers to explore the mechanical properties of lattice structures with ease. Metafold's simulation approach combines an explicit, quasi-static and meshless simulation approach with fast and accurate algorithms. This enables users to efficiently obtain stress distribution at different displacements as illustrated in Figure 4.
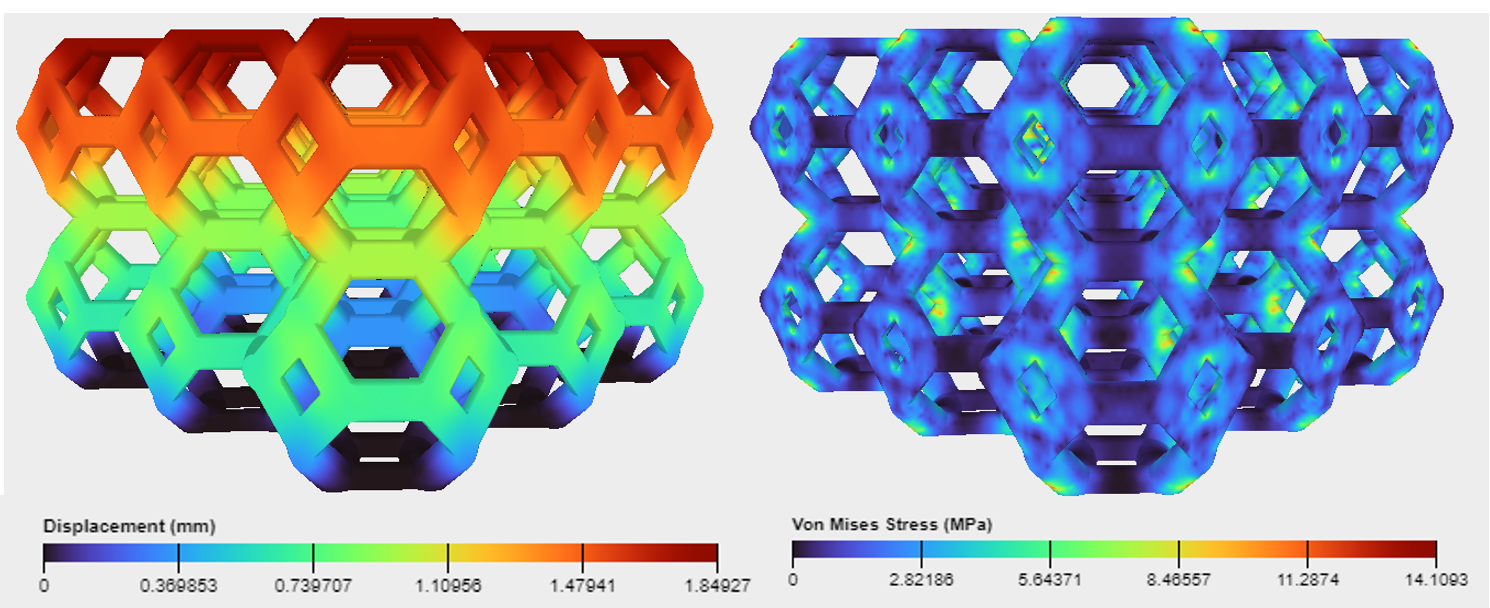
By leveraging the expertise of renowned material suppliers like BASF®, Metafold ensures that its simulations are based on validated material models. This collaboration enables engineers to confidently analyze 3D printed lattice structures, gaining valuable insights into their performance. Metafold's user-friendly platform and free account sign-up option make it accessible to both seasoned professionals and aspiring researchers in the field.
[1] Ashby, Michael F. "The properties of foams and lattices." Philosophical Transactions of the Royal Society A: Mathematical, Physical and Engineering Sciences 364.1838 (2006): 15-30.