In a recent article, Peter Zelinski argues that additive manufacturing (AM) has the potential to revolutionize manufacturing by enabling ‘toolingless’ production. In response to recent discouraging market changes and reports, he reminds us to take a long view, and that the promise of AM to revolutionize manufacturing is too exciting to be extinguished.
I wholeheartedly agree with Zelinski’s position, but add the clarification that AM allows tooling to become digital. This paradigm shift from traditional, tool-based manufacturing to a more digital approach offers significant advantages in terms of speed, efficiency, and sustainability. However, this transition also places new demands on the digital tooling that replaces its physical predecessor.
Benefits of Digital Tooling for Additive Manufacturing
Shifting tooling from physical to digital allows manufacturers to be more nimble, with advantages for the bottom line of the business through optimization and reduced impact on the planet.
Enhanced Production Speed and Agility
The creation of physical tooling can be a significant bottleneck and expense in the manufacturing process. The transition to digital tooling means that the only requirement to produce a part is its digital representation (model, blueprint or ‘recipe’ of some kind). This shift significantly reduces the total time from design to production, as changes can be made rapidly in the digital file without the need to alter or create new physical tools. Moreover, additive manufacturing allows for rapid prototyping and on-demand production, drastically reducing the development cycle and inventory requirements. 3D printing can either directly manufacture the end-use product, or it can be used to rapidly create the tooling (e.g. molds, dies and jigs) required for production using traditional means.
Sustainable Manufacturing and Optimized Application-Specific Parts
Unlike traditional subtractive methods, additive manufacturing adds material only where needed, minimizing waste and promoting sustainability. More importantly, additive manufacturing also enables the creation of lightweight, optimized structures that are impossible to produce with traditional methods. There are excellent examples of high performance heat exchangers, intensified chemical reactors and high-strength low-weight parts in airplanes. These application-specific process improvements pay dividends over the lifetime of part use.
Requirements of Digital Tooling for Additive Manufacturing
While additive manufacturing eliminates the need for physical tooling, it places new demands on the digital tooling that replaces it. The effectiveness of this technology hinges on the capabilities of the digital tools used to design, analyze, and prepare models for printing.
While the design and production of physical tooling can take weeks or even months, the development of digital tooling is also nontrivial.
Digital tooling in additive manufacturing necessitates robust geometry handling capabilities. Traditional CAD software is often not suited for this task due to fundamental limitations with explicit geometry representations such as triangle meshes or BREP models. A new generation of engineering software (including Metafold’s platform) for additive manufacturing use implicit representation that allow for ultra-fast and ultra-robust geometry creation and manipulation, even for highly complex or intricate structures.
Additional software may include sophisticated slicing algorithms to translate 3D models into printable layers. This includes material optimization and quality control mechanisms to ensure the functionality and viability of the final product.
Further considerations may include secure digital warehousing, long term digital storage and long term part ‘memory’ (e.g. what are the engineering parameters and requirements that informed the creation of the part?).
Excellence in Manufacturing Will be Defined by the Software Stack
Our world is a product of tooling. Great companies are defined by their tooling — For example the iconic Converse brand is captured by the unique shape of the midsole mold; IKEA Poang chairs by their characteristic bent wood frames. The transition to digital tooling will be similarly company-defining, but now it is the software stack that will determine a company’s success. As manufacturing (slowly!) shifts toward the digital, building the right software infrastructure that future-proofs production is a critical step in maintaining a competitive market position.
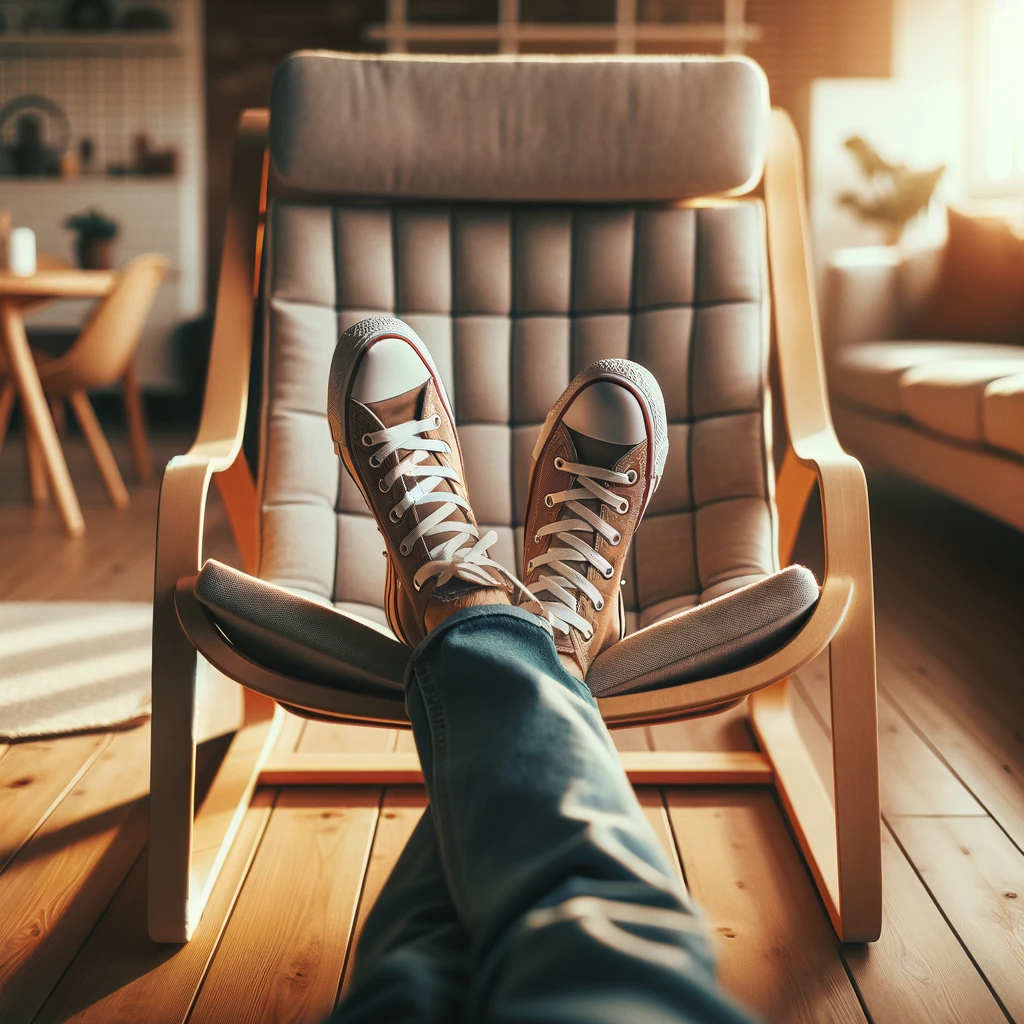
Selecting a Software Stack for Digital Manufacturing
Here are a few questions to consider when choosing a software stack to support digital tooling for manufacturing.
- Is it fast? While software is assumed to be faster than physical manufacturing, the reality is that design tools can become slow when faced with heavy geometric computations. Software that worked well to design traditionally manufactured parts may not be well suited for digital fabrication. Volumetric (or implicit) modelling platforms take a different computational approach that ensure geometry processing is not a bottleneck.
- Is it secure? Traditionally companies could be assured of some competitive protection through securing their physical assets. Security in software and data management is a critical aspect of digital tooling. On premise software is not necessarily the correct answer, especially as the need for cloud compute and internal data sharing/collaboration increases.
- Does it integrate with other elements of the software and production stack? To create a truly customized software stack may require more than importing and exporting. Automation and communication can be achieved when APIs are available.
- Can it scale? Digital manufacturing offers the possibility for end-customers to interact directly with a company’s software prior to interacting with their physical goods. Is the software stack ready for this shift, even if it occurs well in the future?
- Does it allow for resource optimization? Distributed, hybrid work is the new normal, and even the manufacturing companies can take advantage of skilled global labour through cloud-based software stacks. This may emerge as a defining competitive advantage for the modern manufacturing environment.